智能模拟仿真软件在工业制造中的高效优化与精准预测应用技术文档
1. 技术概述
智能模拟仿真软件通过数字孪生、虚拟调试、多物理场耦合等技术,为工业制造提供从设计到生产的全生命周期优化与预测能力。其核心目标是通过虚拟环境对生产线、物流系统、设备维护等环节进行建模与仿真,降低试错成本,提升效率与质量。
用途:
生产线优化:通过动态仿真分析瓶颈工序,优化资源配置与生产节拍。
物流规划:模拟仓储布局、物料搬运路径及AGV调度,降低物流成本。
设备维护预测:结合设备运行数据与仿真模型,预测故障周期并制定维护策略。
工艺验证:在虚拟环境中测试焊接、装配等工艺参数,确保实际生产可行性。
技术优势:
高效优化:支持多场景并行仿真,快速迭代设计方案,如吉利汽车通过仿真将生产误差控制在0.5秒以内。
精准预测:融合AI算法与大数据的动态模型,可预测能耗、废品率等关键指标,误差率低于5%。
2. 核心功能模块与技术实现
智能模拟仿真软件的功能模块涵盖建模、分析、优化全流程,具体包括:
2.1 建模与数据集成
三维几何建模:支持STEP、IGES等格式导入,并通过布尔运算构建复杂模型(如汽车冲压模具)。
网格划分与简化:提供四面体/六面体网格划分功能,并优化缺陷特征(如重叠面、缝隙)以提高计算效率。
多源数据融合:集成ERP、MES系统中的生产数据,实现虚实联动。
2.2 仿真与分析引擎
多物理场耦合:支持结构力学(FEA)、流体力学(CFD)、电磁场的联合仿真,如汽车碰撞场景中应力与空气动力学的协同分析。
实时动态仿真:基于Unity/Unreal引擎渲染三维场景,模拟设备振动、温度分布等实时变化。
2.3 优化与决策支持
参数自动调优:通过遗传算法或强化学习优化工艺参数,如注塑模具的冷却时间减少15%。
风险叠加分析:评估多项目叠加后的整体风险(如爆炸事故的社会影响),并生成防护建议。
3. 典型应用场景分析
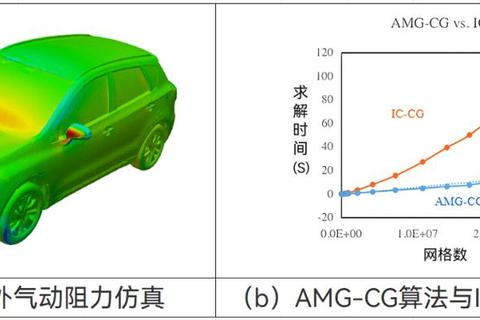
3.1 汽车制造
虚拟调试:西门子Process Simulate将现场调试时间缩短50%,支持机器人焊接路径规划与碰撞检测。
总装线优化:通过RFID技术追踪车身装配状态,动态调整工位节拍。
3.2 航空航天
飞行器结构验证:Unity 3D模拟真实飞行环境,结合CFD分析机翼气动性能,训练误差降低30%。
3.3 电子制造
SMT生产线仿真:预测贴片机抛料率,优化供料器布局,节省材料成本10%以上。
4. 软件使用流程说明
4.1 模型构建阶段
1. 几何导入:将CAD模型导入软件,检查并修复几何缺陷(如孔洞或非流形边)。
2. 网格划分:根据仿真类型选择网格密度,例如流体仿真需边界层加密。
4.2 仿真参数设置
物理场选择:定义材料属性(如弹性模量、泊松比)与边界条件(如固定约束、热源)。
动态事件配置:设置AGV路径、设备故障触发逻辑等。
4.3 运算与结果分析
高性能计算(HPC):调用GPU加速(如NVIDIA OptiX),单次仿真时间从小时级降至分钟级。
可视化输出:生成应力云图、温度分布动画及风险热力图。
5. 系统配置要求
5.1 硬件配置
CPU:Intel Xeon或AMD EPYC系列,主频≥3.0GHz,核心数≥16(推荐AVX-512指令集)。
GPU:NVIDIA RTX A6000或同等级计算卡,显存≥48GB(支持CUDA并行计算)。
内存与存储:≥128GB DDR5内存,NVMe SSD阵列(读取速度≥7GB/s)。
5.2 软件环境
操作系统:Windows Server 2022或Linux CentOS 8.3。
依赖库:ANSYS Mechanical APDL、OpenFOAM(流体求解器)、Python 3.9(脚本扩展)。
6. 未来发展趋势
智能模拟仿真软件在工业制造中的高效优化与精准预测应用将进一步融合AI与边缘计算技术:
AI增强仿真:基于扩散模型生成高精度合成数据,减少对物理实验的依赖。
云边协同:通过5G将仿真任务分发至边缘节点,实现实时反馈(如数字孪生工厂的毫秒级响应)。
绿色制造:优化能耗模型,预测碳排放并推荐低碳工艺(如钢铁行业石灰石回收优化案例)。
智能模拟仿真软件在工业制造中的高效优化与精准预测应用已成为智能制造的核心驱动力。通过本文的技术解析与案例说明,企业可结合自身需求选择适配工具,构建从虚拟验证到实际生产的闭环体系,最终实现降本增效与竞争力提升。
相关文章:
文章已关闭评论!