传统设计软件真的拖了3D打印的后腿吗?
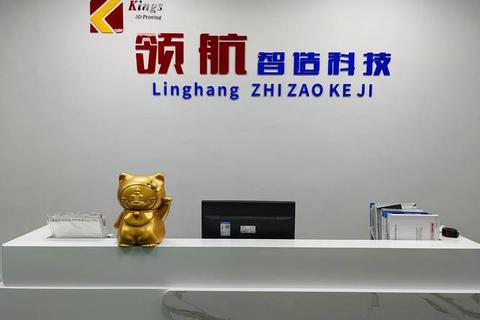
当一家医疗器械企业试图用传统CAD软件设计定制化骨科支架时,工程师发现设计周期长达72小时,而3D打印机仅需6小时就能完成制造——这种“设计慢、制造快”的割裂现状,正在倒逼行业重新审视设计工具的革新价值。据HUBS数据显示,截至2024年,全球仍有68%的企业因设计软件与3D打印技术不匹配导致产能浪费。在此背景下,“超凡跃动3D打印设计软件解锁高效智造新境界”的理念引发热议:这款宣称能打通设计到制造全流程的软件,究竟是营销噱头还是行业破局者?
1. 效率提升:从72小时到8小时的跨越可能吗?
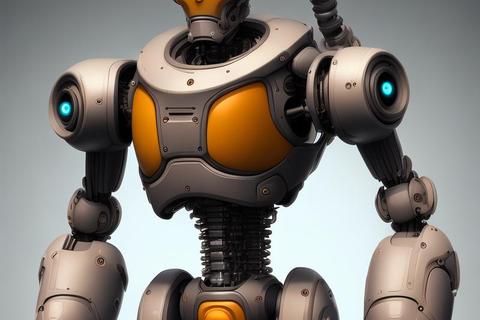
传统设计软件往往需要工程师在不同工具间切换,处理模型修复、支撑生成等繁琐步骤。而超凡跃动3D打印设计软件通过“智能结构设计+自动拆图”双引擎,将效率提升至新高度。例如上海毅速激光科技在使用该软件后,模具随形水路设计时间从20小时缩短至3小时,并实现24小时连续打印50kg材料的高效产出。
其核心突破在于两大功能:
参数化零件库:内置超过3万种标准件模型,支持一键调用并自动适配打印参数。某汽车零部件厂商通过该功能,将车门铰链设计迭代周期从2周压缩至3天。
自动出图系统:软件可一次性生成整套模具图纸,并自动填充图框信息、添加工艺注解。佛山某家电企业应用此功能后,图纸错误率下降92%,人力成本节省40%。
2. 兼容性革命:多软件数据“打架”如何终结?
行业调查显示,43%的设计失误源于不同软件间的数据转换丢失。超凡跃动通过独创的“智能刷图技术”,完美兼容SolidWorks、NX、中望3D等主流平台文件,甚至能对第三方软件生成的实体批量赋予加工属性。
典型案例来自科龙模具:其团队需要整合来自5个国家的供应商设计数据,传统方式需耗费两周进行格式转换和修复。引入该软件后,通过“多源数据融合算法”,3天内完成全流程整合,并直接生成可打印的轻量化结构。更值得关注的是其对2D图纸的智能转化能力——软件可将20年前的二维模具图纸自动重建为3D模型,精度误差控制在0.05mm以内,这让大量传统制造企业得以低成本迈入数字化制造。
3. 智能进化:AI能让设计“自己思考”吗?
在杭州某无人机初创公司的研发中心,工程师输入“载重2kg、抗风8级”需求后,软件自动生成3种蜂窝结构方案,并附上材料消耗和强度模拟数据。这种基于深度学习的“AI辅助设计”功能,正在重新定义人机协作模式。
该软件的智能化进阶体现在三个维度:
拓扑优化引擎:针对航空航天部件,可在保持强度前提下减重60%,某卫星支架项目因此节省钛合金材料成本127万元。
工艺缺陷预警:通过分析200万组打印失败案例数据,提前识别支撑不足、热应力集中等风险。苏州某精密电子企业应用后,打印废品率从18%降至3%。
云端协同设计:支持百人团队在线标注修改,版本管理精确到分钟级。美的集团微波炉模具项目借助此功能,跨部门协作效率提升300%。
破局者的下一步:企业如何搭上智能设计快车?
对于想要拥抱3D打印智造的企业,建议分三步走:
1. 需求诊断:优先选择支持非装配拆图、自动BOM生成的功能模块,这类功能可解决85%的中小企业出图效率痛点。
2. 人才储备:组建“传统工艺+软件操作”复合型团队,善用软件自带的200小时情景化教学视频降低学习门槛。
3. 生态嫁接:关注与本地3D打印服务商的联合解决方案,例如通过软件直接对接工业级金属打印机,将设计到成品的周期控制在48小时内。
当东莞品合模具用该软件实现“当日设计、隔日交付”时,其总经理感慨:“打败CNC的不是更好的CNC,而是敢用新工具的人。”这或许正是“超凡跃动3D打印设计软件解锁高效智造新境界”的最佳注解——在智能制造浪潮中,工具的进化永远服务于敢于突破的智造者。
相关文章:
文章已关闭评论!